Generative design is revolutionizing hardware engineering by using AI algorithms to explore thousands of design possibilities and automatically create optimized components. Unlike traditional CAD—which starts from a human-created model—generative design begins with project goals and constraints (strength, weight, cost, etc.) and has AI generate many solutions. Engineers can then choose and refine the best option. This approach can dramatically reduce weight, cut material usage, and improve performance. For example, AI-driven design helped a team produce an optimized e-bike chassis with a light, organic lattice structure. In one real-world case, General Motors used generative design and 3D printing to remake a seat-bracket: the new part was 40% lighter than the original. Such AI-designed geometries solve complex challenges that manual design often cannot.
Fig: A bicycle frame designed with generative AI. The intricate lattice (developed by Airbus’s APWorks) minimizes weight while maintaining strength, a result that would be hard to conceive manually.
Generative algorithms also optimize for thermal performance, material efficiency, and ergonomics. They can mimic nature’s branching patterns to improve heat dissipation or tailor shapes to a user’s hand. For instance, researchers have shown that branching “tree-like” fin structures (inspired by natural cooling systems) greatly improve heat transfer. AI can similarly fine-tune air-flow channels in enclosures or heat sinks for electronics, leading to better cooling without added material.
Key Technologies and Tools
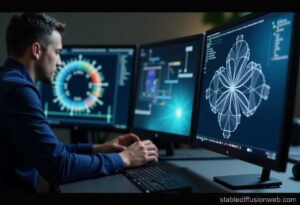
Modern generative design relies on advanced software platforms. Notable tools include:
Autodesk Fusion 360 (Dreamcatcher) – One of the pioneers, Autodesk’s Project Dreamcatcher can automatically generate thousands of CAD layouts from high-level goals. Fusion 360 now incorporates these features in the cloud, letting designers iterate rapidly on consumer electronics enclosures and PCB placements.
nTopology (nTop) – A computational design platform that gives engineers granular control. nTop allows users to define custom optimization logic and simultaneously optimize for weight, strength, and thermal requirements. It has been used to redesign jet-engine and aerospace parts: for example, an nTop-generated hydraulic clamp for an F-16 was twice as stiff yet remained manufacturable by 3D printing.
Cadence Cerebrus AI – A chip-design tool that uses reinforcement learning. Cerebrus automates low-level decisions in SoC and PCB layout, optimizing power, performance, and area. It has helped customers shrink chip die sizes and improve energy efficiency beyond human designs.
Synopsys DSO.ai – A “first-of-its-kind” AI engine for chip design. DSO.ai explores vast design spaces of logic and layout, using reinforcement learning to meet PPA (power-performance-area) targets faster. It integrates with Synopsys’s Fusion Compiler to automate many physical design choices and rapidly converge on high-quality solutions.
Cadence Allegro X AI – An AI-enhanced PCB layout platform. Allegro X automates component placement and routing for complex boards, reducing design time from days to minutes. The tool ensures the board meets electrical and manufacturing rules. It has demonstrated up to 10× faster turnaround for PCB design while maintaining or improving quality.
Others – Tools like Altair Inspire, Siemens NX, and emerging startups (e.g. Cadstrom, Camfer) are also developing AI-assisted design. These platforms help with topology optimization, rule-based generation, and even natural-language-driven design queries.
Real-World Applications in Hardware

Generative AI is already applied across hardware domains:
Structural Lightweighting: AI-generated parts often use internal lattices and organic shapes to minimize weight. (See the e-bike frame above.) In automotive and aerospace, this leads to huge savings: an Airbus cabin partition redesigned by AI was 45% lighter and 60% stiffermedium.com ↗️. General Motors’ generative-design seat bracket example cut weight by 40% and reduced part count.
Thermal Optimization: For electronics cooling, algorithms create tree-like heat-sink geometries that improve airflow and heat removalelectronics-cooling.com ↗️. Toyota researchers use AI to generate branching fins for natural convection sinks, dramatically boosting heat transfer. In practice, companies can let AI tailor a heat exchanger’s shape to the exact thermal load and space constraints, outperforming off-the-shelf designs.
Space Saving & Packaging: When fitting PCBs and components into tight enclosures (smartphones, wearables, satellites), generative design can pack boards in 3D or suggest new PCB shapes. Fusion 360’s “design projection” shows how a PCB and its enclosure can be co-designedautodesk.com ↗️. Cadence’s Allegro X ensures that PCBs meet electrical rules, while AI could explore non-rectangular board shapes or foldable circuits. Startups are also tackling PCB design directly: for example, Cadstrom’s AI (Sigma Engine) uses physics and generative models to catch layout errors early, potentially eliminating up to 66% of design revisions.
Ergonomics and Customization: AI can tailor device housings to human form or specific tasks. For example, a hand tool’s handle might be morphed by generative software to fit the user’s grip, balancing comfort and strength. Adidas famously used generative design for a custom shoe midsole that adapts to an individual’s foot shapemedium.com ↗️. While the upfront design is AI-driven, engineers still ensure the result meets safety and usability standards.
Each of these applications highlights how AI-designed geometry outperforms traditional CAD. Engineers no longer have to manually sketch dozens of variants; the software iterates them automatically. The NVIDIA technical blog observes that AI-driven generative design “enables engineers to generate multiple design options… reducing the need for physical iterations and significantly accelerating the design process”developer.nvidia.com ↗️. This massively parallel exploration (sometimes hundreds of thousands of concepts) yields innovative shapes that human intuition alone might never conceive.
AI in Electronics and User Interfaces
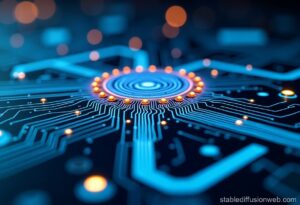
Modern hardware is a blend of electronics and software, and AI is entering both worlds:
PCB & Chip Co-Design: Tools are emerging to design PCBs and chips in concert with mechanical enclosures. Autodesk Fusion lets teams move “seamlessly from mechanical enclosures to electronics”autodesk.com ↗️, using a unified 3D CAD environment. Cadence Allegro X AI, mentioned above, automates PCB placement and routing while running signal-integrity and thermal analysesventurebeat.com ↗️. This “co-design” ensures a board will actually fit in its case and meet electrical requirements. On the IC side, Cadence Cerebrus and Synopsys DSO.ai similarly tie together logic synthesis, layout, and physical constraints, finding chip floorplans a human might missbusinesswire.com ↗️. Startups like Cadstrom go further: their AI engine uses physics-based models to validate entire electronic designs before they hit the prototype phasepcdandf.com ↗️, catching errors early and reducing costly respins.
User Interface (UI/UX) Design: Generative AI is also changing digital interfaces. “Generative UI” (GenUI) refers to interfaces that adapt in real time to each user’s context and goalsnngroup.com ↗️. For example, Nielsen Norman Group explains that in the future a GenUI “will dynamically create customized user interfaces in real-time,” tailoring layouts and options to the individualnngroup.com ↗️. Instead of one-size-fits-all screens, AI could rearrange buttons, suggest content, or even generate entire form fields on the fly. Tools like Uizard or Galileo AI already use machine learning to generate prototypes from sketches or text prompts, and big models (like GPT-4) can assist in wireframing and code for web/app UI. This shifts the designer’s role from manually placing every button to defining outcomes and constraints for the AI to achievenngroup.com ↗️. Early research shows generative UIs can vastly personalize experiences – for instance, interfaces that display only the most relevant tools based on what a user is trying to accomplishnngroup.com ↗️. While still a nascent field, this trend points to future hardware products (like smart appliances) with AI-personalized screens and controls.
Industry Adoption and Trends
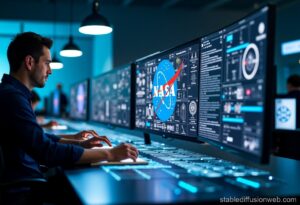
Generative AI in hardware is rapidly gaining traction across the U.S. tech landscape:
Aerospace & Defense: NASA’s Jet Propulsion Lab (JPL) has long studied generative design for spacecraft. In one initiative with Autodesk, JPL sought >30% performance improvement in a lander design – a goal traditional methods wouldn’t meet. In space and aviation, every kilogram counts, so organizations like NASA and Airbus openly share successes in AI-lightweighting. SpaceX uses extensive additive manufacturing for Falcon 9 and Starship parts, and engineers likely leverage generative design to optimize those geometries for 3D printing.
Automotive & Consumer Electronics: Companies like GM and Toyota have adopted generative tools for vehicle parts. Consumer-device makers (e.g. smartphone or wearables) often use AI for structural components and to pack electronics densely. While Apple has not publicly detailed its use of generative design, it aggressively uses AI on-device (e.g. “Apple Intelligence” for software) which hints that similar methods could be applied to hardware R&D. NVIDIA, which supplies chips and software for AI, published a 2025 blog on how AI-driven generative design can transform manufacturing workflows. In short, industry leaders view this technology as a key competitive advantage.
Startups and Venture Capital: A wave of hardware-focused startups is embracing AI. For example, Cadstrom (founded 2023) raised $6.8M to automate PCB design validation. Y Combinator is incubating ventures like Camfer, “building the world’s first AI mechanical engineer” to collaborate on CAD tasks. Investors are increasingly betting on “AI for hardware” platforms that can speed product development. According to Brookings research, generative AI could disrupt over 30% of tasks across many jobs, so engineers are quickly learning to use these tools to stay productive. Overall, U.S. startups and tech giants alike are integrating AI into design pipelines, from ideation through manufacturing.
Challenges and Limitations
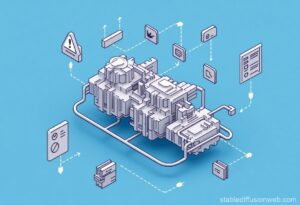
Despite its promise, AI-driven hardware design faces hurdles:
Manufacturability: AI often produces organic, complex shapes that are hard to manufacture with conventional methods. Many generative solutions require additive manufacturing (3D printing) or complex tooling. Imposing manufacturing constraints during generation can limit performance; otherwise, engineers must manually simplify or split parts post-hoc.
Verification and Safety: AI designs can have hidden features (internal voids, stress concentrations) that are hard to inspect. Ensuring reliability, especially in safety-critical industries, still requires traditional analysis and testing. Moreover, AI models must capture all relevant constraints (material limits, load conditions, EMI for PCBs, etc.), which isn’t trivial. If not fully accounted for, AI-generated parts might fail unexpectedly.
Intellectual Property (IP): The question “who owns a design created by AI?” is unsettled. Complex AI-generated shapes may not be directly patentable, and IP protection for products built that way is still an evolving legal area. This complicates commercialization when multiple teams or tools contribute to a design.
Technical Maturity: Generative AI tools are improving but aren’t magic. They rely on good input constraints and data. Engineers often need to iterate with AI (tuning objectives) and verify outcomes. Integration into legacy CAD workflows can be uneven, and adoption requires training teams on new processes.
In short, while generative design automates much of the heavy lifting, engineers must guide the process and apply traditional engineering judgment to finalize and qualify designs.
Future Outlook
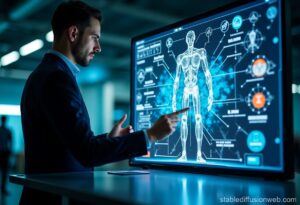
The trajectory is clear: AI will play an ever-larger role in hardware engineering. Design-to-production pipelines are likely to become more integrated and iterative. For example, AI agents could generate a prototype design, simulate it, refine it, and even suggest manufacturing steps in a closed loop, slashing development time. “AI-driven design spaces” will blur the line between design and analysis: as NVIDIA notes, engineers will explore hundreds of thousands of concepts simultaneously, a scale impossible before.
Job roles will evolve but not vanish. Brookings researchers estimate generative AI could disrupt 30%+ of work tasks, but they emphasize workers will need to adapt rather than be replaced. In hardware, we expect new roles such as “AI design specialist” or “automation engineer” to emerge. Engineers will spend less time on routine drafting and more on setting up AI-driven workflows, defining objectives, and reviewing AI-proposed solutions. Academia and industry are already discussing the need to train engineers to collaborate with AI tools.
Overall, generative AI is not replacing human ingenuity but augmenting it. The technology promises faster innovation cycles and highly optimized products. Companies that embrace these tools may leap ahead in efficiency and product performance. While challenges remain in IP, verification, and manufacturing, early adopters are proving the concept: from lightweight rockets to next-generation chips, AI-designed hardware is moving from concept to reality. As this trend grows, we can expect hardware development to look increasingly like software agile development – with AI as a key “team member” accelerating each design sprint.